Innovative wood based composite for compression moulding processes
3DF allows a world of design possibilities: customized deep structures, elegant arcs and curves. Technical and functional aspects such as screw head immersions and embedded handles are also possible with a single operation. The specific formulation of 3DF allows that with the action of temperature and pressure it can be shaped, and different final densities and thicknesses can be achieved according to project needs.
The surface achieved after compression is perfect for lacquering and powder coating. In the compression process the surfacing material, such as flexible CPL, foil and venner, can also be included achieving a final decorative product in one single step. The product gives you design freedom to projects combined with the advantages of a sustainable and controlled wood based panel with very low formaldehyde emissions.
Whether it’s applied in furniture fronts, doors, seats, wall panelling or in other applications 3DF presents several advantages when compared to the alternatives.
In fact, its moulding properties allow to get deep and complex structures and curve shapes on a faster and more productive way than with other materials.
This productivity improvement happens not only due to low cycle times needed to process 3DF but also due to the non requirement of a cooling step after moulding.
Also the moulding process associated to 3DF processing presents advantages when compared to the conventional methods normally used to achieve the same structures: the compression moulding process ensures a dust free environment and virtually eliminates the generated waste, while at the same time delivers a highly compressed smooth surface, perfect for lacquering.
3DF is therefore the best option for turning your most demanding designs into reality with maximum flexibility and minimum effort.
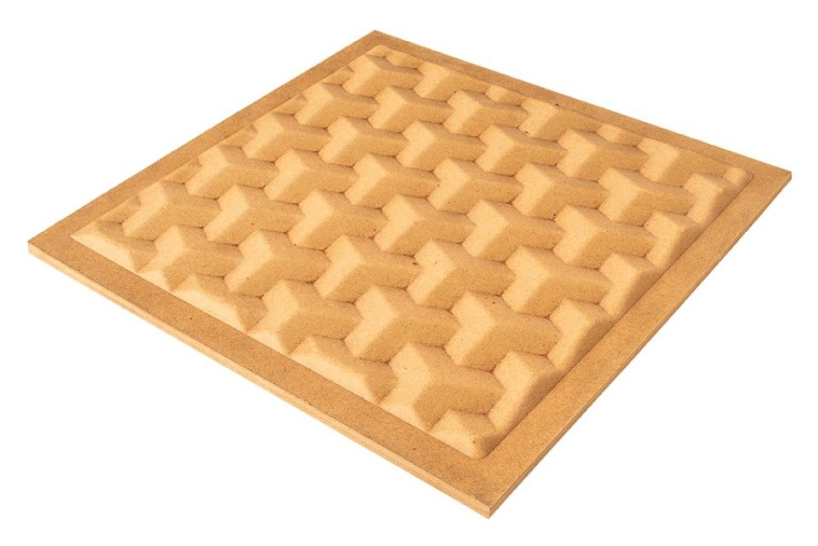
Features
Durable and sustainable product
Low emissions (NAF classification according to CARB)
Good mechanical properties after compression
High thicknesses achievable without visible joints (multiple boards pressed into one)
Features
Benefits
- Time saving
- Lacquering costs saving
- No dust emission when processing
- Deep and detailed structures
- Curves and arcs
- Customized decorative solutions
Applications
3DF is intended for interior applications in horizontal and vertical surfaces where design, appearance, quality and durability are important features.
Product is perfect for interior doors, kitchen doors and front panels, seats, bedheads and furniture fronts, office and living room partitions and curve and acoustic panels.
Applications
Kitchens
Living Rooms
Bedrooms
Offices & Education
Sports & Leisure
Restaurants & Hotels
Health & Wellness
Retail & Exhibitions
Doors
Paneling
Properties
Versatility
Low emissions
Perfect lacquering
Mouldable
Applications
Properties
Instructions for use
For standard moulding shapes and simple structures with 3DF boards a process temperature of 130°C and roughly 2 minutes are needed. To process complex and deep structures it is necessary to increase the moulding press temperature up to 140°C–200°C and extend the pressing time. In addition to the reduced processing times, 3DF is highly stable immediately after pressing, allowing it to be directly processed, giving a positive impact on productivity.
The bending strength of the compressed parts can be increased by raising the pressure and press time. These actions also increase the surface density of moulded part.
On other hand an homogeneous density profile optimizes the internal bond. Due to a closed surface, primer coat layers and lacquer weight can be reduced, achieving the same finishing quality level. In particular the surface of the deeper parts of a moulded panel is much smoother than at a CNC milled MDF. This optimizes the surface coating quality of the deeper areas.
Standard equipment to saw and sand wood based boards can be used to process 3DF. Different embedded compositions can be added to the part if projected in mould design, that allows an easier incorporation of screws and fittings afterwards.